Пористость, неоднородности типа полостей, образующиеся в результате захвата газа во время затвердевания, является распространенным, но обременительным дефектом при сварке MIG, который имеет несколько причин. Он может появиться в полуавтоматических или роботизированных приложениях и в обоих случаях требует удаления и доработки, что приводит к простою и увеличению затрат.
Основной причиной пористости при сварке стали является азот (N2), который попадает в сварочную ванну. При охлаждении ванны жидкости растворимость N2 значительно снижается и N2 выходит из расплавленной стали, образуя пузыри (поры). При гальванизированной/гальванической сварке испаренный цинк может попасть в сварочную ванну, и если не будет достаточно времени для его выхода до затвердевания ванны, он образует пористость. При сварке алюминия вся пористость вызвана водородом (H2), точно так же, как N2 действует в стали.
Сварочная пористость может проявляться снаружи или внутри (часто называемая подповерхностной пористостью). Он также может развиваться в одной точке сварного шва или по всей его длине, что приводит к непрочности сварных швов.
Знание того, как определить некоторые ключевые причины пористости и как быстро их устранить, может помочь улучшить качество, производительность и прибыль.
Плохое покрытие защитным газом
Плохое покрытие защитным газом является наиболее распространенной причиной сварочной пористости, поскольку оно позволяет атмосферным газам (N2 и H2) загрязнять сварочную ванну. Отсутствие надлежащего покрытия может произойти по нескольким причинам, включая, помимо прочего, низкую скорость потока защитного газа, утечки в газовом канале или слишком большой поток воздуха в сварочной камере. Причиной также может быть слишком высокая скорость движения.
Если оператор подозревает, что проблема вызвана плохим потоком, попробуйте отрегулировать расходомер газа, чтобы убедиться в адекватности расхода. Например, при использовании режима распыления должно быть достаточно расхода от 35 до 50 кубических футов в час (кубических футов в час). Сварка при более высокой силе тока требует увеличения скорости потока, но важно не устанавливать слишком высокую скорость. В некоторых конструкциях пистолетов это может привести к турбулентности, которая нарушает покрытие защитным газом.
Важно отметить, что пистолеты разной конструкции имеют разные характеристики потока газа (см. два примера ниже). «Оптимальная зона» расхода газа для верхней конструкции намного больше, чем для нижней конструкции. Это то, что инженер-сварщик должен учитывать при настройке сварочной камеры.
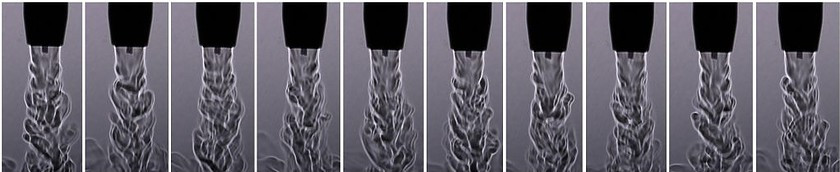
Конструкция 1 показывает плавный поток газа на выходе из сопла.
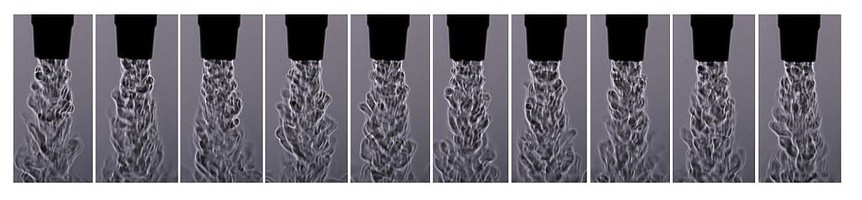
На схеме 2 показано турбулентное течение газа на выходе из сопла.
Также проверьте на наличие повреждений газовый шланг, фитинги и разъемы, а также уплотнительные кольца на штыре питания сварочной горелки MIG. При необходимости замените.
При использовании вентиляторов для охлаждения операторов или деталей в сварочной камере следите за тем, чтобы они не были направлены непосредственно на зону сварки, где они могли бы нарушить газовое покрытие. Установите экран в сварочной камере для защиты от внешнего потока воздуха.
Повторно коснитесь программы в роботизированных приложениях, чтобы убедиться, что между наконечником и заготовкой установлено правильное расстояние, которое обычно составляет от ½ до 3/4 дюйма, в зависимости от желаемой длины дуги.
Наконец, медленные скорости перемещения, если пористость сохраняется, или проконсультируйтесь с поставщиком сварочной горелки для сварки MIG по поводу других компонентов передней части с лучшей защитой от газа.
Загрязнение недрагоценными металлами
Загрязнение недрагоценными металлами — еще одна причина возникновения пористости — от масла и жира до прокатной окалины и ржавчины. Влага также может способствовать этому нарушению непрерывности, особенно при сварке алюминия. Эти типы загрязнений обычно приводят к внешней пористости, видимой оператору. Оцинкованная сталь более склонна к подповерхностной пористости.
Для борьбы с внешней пористостью обязательно тщательно очистите основной материал перед сваркой и рассмотрите возможность использования сварочной проволоки с металлическим сердечником. Этот тип проволоки имеет более высокий уровень раскислителей, чем сплошная проволока, поэтому он более устойчив к любым оставшимся загрязнениям на основном материале. Всегда храните эти и любые другие провода в сухом, чистом помещении с температурой, аналогичной температуре установки или немного выше. Это поможет свести к минимуму образование конденсата, который может привести к попаданию влаги в сварочную ванну и вызвать пористость. Не храните провода на холодном складе или на открытом воздухе.
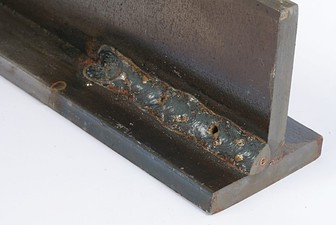
Пористость, неоднородности типа полостей, образующиеся в результате захвата газа во время затвердевания, является распространенным, но обременительным дефектом при сварке MIG, который имеет несколько причин.
При сварке оцинкованной стали цинк испаряется при более низкой температуре, чем плавится сталь, а высокие скорости перемещения приводят к быстрому замерзанию сварочной ванны. Это может привести к улавливанию паров цинка в стали, что приведет к пористости. Боритесь с этой ситуацией, контролируя скорость движения. Опять же, рассмотрим специально разработанную (формула флюса) металлопорошковую проволоку, которая способствует выходу паров цинка из сварочной ванны.
Засорены и/или форсунки недостаточного размера.
Засоренные и/или сопла недостаточного размера также могут стать причиной пористости. Сварочные брызги могут накапливаться в сопле, на поверхности контактного наконечника и диффузора, что приводит к ограничению потока защитного газа или к его турбулентности. В обеих ситуациях сварочная ванна остается без недостаточной защиты.
Ситуацию усугубляет то, что сопло слишком мало для данного применения и более склонно к большему и быстрому образованию брызг. Сопла меньшего размера могут обеспечить лучший доступ к стыку, но также препятствуют потоку газа из-за меньшей площади поперечного сечения, предусмотренной для потока газа. Всегда помните о разнице между выступом (или углублением) контактного наконечника и сопла, поскольку это может быть еще одним фактором, влияющим на поток защитного газа и пористость при выборе сопла.
Имея это в виду, убедитесь, что сопло достаточно большое для применения. Обычно для применений с высоким сварочным током и использованием проволоки большего диаметра требуется сопло с большим диаметром отверстия.
При полуавтоматической сварке периодически проверяйте наличие сварочных брызг в сопле и удаляйте их с помощью сварочных клещей или при необходимости замените сопло. Во время этой проверки убедитесь, что контактный наконечник находится в хорошей форме и что газовый диффузор имеет чистые газовые отверстия. Операторы также могут использовать состав для защиты от брызг, но они должны следить за тем, чтобы не окунать сопло в состав слишком глубоко или на слишком долгое время, поскольку чрезмерное количество состава может загрязнить защитный газ и повредить изоляцию сопла.
При роботизированной сварке приобретите станцию для очистки сопел или расширитель для борьбы с накоплением брызг. Это периферийное устройство очищает сопло и диффузор во время обычных производственных пауз, не влияя на время цикла. Станции очистки форсунок предназначены для работы в сочетании с распылителем против брызг, который наносит тонкий слой состава на передние компоненты. Слишком много или слишком мало жидкости для защиты от брызг может привести к дополнительной пористости. Добавление струи воздуха к процессу очистки форсунок также может помочь в удалении брызг с расходных материалов.
Поддержание качества и производительности
Контролируя процесс сварки и зная причины пористости, можно относительно легко реализовать решения. Это может помочь обеспечить более длительное время горения дуги, качественные результаты и выпуск большего количества качественных деталей в процессе производства.
Время публикации: 02 февраля 2020 г.